St Augustine St Johns County 904-824-7144
Orange Park Clay County 904-264-6444
Jacksonville Beaches Duval County 904-246-3969
Fernandina Nassau County 904-277-3040
Macclenny Baker County 904-259-5091
Palm Coast Flagler County 386-439-5290
Daytona Volusia County 386-253-4911Jacksonville Duval County 904-346-1266
Serving all of Florida and Georgia at 904-346-1266
EMAIL ASAPDEAN@GMAIL.COM (feel free to email your bidding packages here)
MONTHLY SERVICE AVAILABLE
MONTHLY SERVICE CONTRACTS
LIFT STATION INSPECTIONS
LICENSED LIFT STATION COMPANY
INSURED
FREE ESTIMATES
STATE OF FLORIDA CERTIFIED PLUMBING CONTRACTOR
CFCO56659
LIFT STATION PUMPS
LIFT STATION CRANE
CONTROL PANELS
RAILS
we have a team of experienced individuals who come into your plant OR BUSINESS with a fresh pair of eyes. The system is checked from influent to effluent. System optimization, equipment efficiency and operational excellence are key components explored. Key Benefits Equipment efficiency Total Cost of Operation reductions Reliability and safety
An onsite audit is conducted to examine system parameters, process controls, and current monitor and control procedures. A physical walk-through is conducted, process flow diagrams are examined, previous design criteria are examined and current standard operating procedures are evaluated along with data logs.
NOW HIRING
CLICK HERE TO apply for a job online
CLICK BELOW AND PLACE A WORK ORDER
IN OUR AUTOMATED WORK ORDER SYSTEM
http://www.asap-plumbing.com/Submit_a_New_Work_Order/submit_a_new_work_order.php
Serving the entire Jacksonville area including the following communities:
- Argyle Forest
- Arlington
- Asbury Lake
- Avondale
- Baldwin
- Bayard
- Baymeadows
- Beauclerc
- Bryceville
- Callahan
- Cecil Field
- Cedar Point
- Cunningham
- Dinsmore
- Durkeeville
- Five Points
- Fruit Cove
- Ft Caroline
- Golfair
- Greater Jacksonville
- Herlong
- Hidden Hills
- Hilliard
- Jacksonville
- Jacksonville Beach
- Jacksonville Heights
- Jacksonville International Airport
- Julington Creek
- Lake Shore
- Lakeside
- Loretto
- Macclenney
- Mandarin
- Marietta
- Maxville
- Middleburg
- Murray Hill
- New Berlin
- Nocotee
- Northside Jacksonville
- Oak Leaf
- Ocean Way
- Ortega
- Palencia
- Palm Valley
- Pecan Park
- Pottsburg Creek
- Queens Harbor
- Riverside
- San Jose
- San Marco
- Soutel
- Southbank
- Southpoint
- Southside Jacksonville
- Springfield
- St Johns
- St Nicholas
- Starke
- Switzerland
- Talbot Island
- Tallyrand
- Timuquana
- Westside Jacksonville
- Whitehouse
- World Golf Village
- Yulee
Wastewater lift stations are used to help transport liquid wastewater from homes and businesses across the City to the treatment plant for processing and cleaning.
Lift Stations
Sewage lift stations are by definition installed in a difficult operating environment. The commonly used prefabricated steel “can” stations are constantly subjected to a corrosive environment on both the interior and exterior of the station. Because these structures are out of sight they often do not receive the type of care and maintenance needed to protect steel surfaces.
ignificant problem many times with lift stations is odor generation. In addition to concerns for sewer personnel exposed to accumulated gases, sewer gases left to accumulate in air-tight environments can create additional toxic gases and underground potential for explosion, stagnation, and dead space in lines. Aeration is an option to reduce odor. Many ODORS accumulate because of oxygen-deficient environments. The cost to retrofit old sewer systems (lines, stations, can be astronomical for a municipality. Sometimes chemicals such as sodium nitrate are added to increase oxygen content in the water and provide the bacteria an alternate oxygen source when free oxygen from mechanical sources is not available. This prevents H2S formation from facultative or anaerobic bacteria. Pine Scented blocks also have been added to neutralize odors so that neighbors are not complaining.
Grease
Fats, oil and grease – – also called FOG in the wastewater business – – can have negative impacts on wastewater collection and treatment systems. Most wastewater collection system blockages can be traced to FOG. Blockages in the wastewater collection system are serious, causing sewage spills, manhole overflows, or sewage backups in homes and businesses. With the increase in fast food restaurants, many municipalities are having problems with an increase in grease build-up in their lift stations.
Why is grease a problem?
In the sewage collection and treatment business Grease is singled out for special attention because of its poor solubility in water and its tendency to separate from the liquid solution.
Large amounts of oil and grease in the wastewater cause trouble in the collection system pipes. It decreases pipe capacity and, therefore, requires that piping systems be cleaned more often and/or some piping to be replaced sooner than otherwise expected. Oil and grease also hamper effective treatment at the wastewater treatment plant. Grease is the number one cause of foaming and bulking, especially Nocardia and M. parvicella.
Grease in a warm liquid may not appear harmful. But, as the liquid cools, the grease or fat congeals and causes nauseous mats on the surface of settling tanks, digesters, and the interior of pipes and other surfaces which may cause a shutdown of wastewater treatment units.
Bioaugmentation Solutions for Lift stations, Wet Wells and Collection Systems
Solid block biological products that are specifically formulated and packaged for use in lift stations and large restaurant grease traps to remove grease build-up and help increase degradation capabilities.
This biological product is a high strength formulation developed to degrade fats oils and grease quickly. It can be used in restaurants, grease traps and drain fields where food based grease is a problem.
This product is an improved biological product, specifically formulated and packaged for use in sewers to help degrade grease build-up and stop blockage.
we have a team of experienced individuals who come into your plant with a fresh pair of eyes. The system is checked from influent to effluent. System optimization, equipment efficiency and operational excellence are key components explored. Key Benefits Equipment efficiency Total Cost of Operation reductions Reliability and safety
An onsite audit is conducted to examine system parameters, process controls, and current monitor and control procedures. A physical walk-through is conducted, process flow diagrams are examined, previous design criteria are examined and current standard operating procedures are evaluated along with data logs.
United States
Environmental Protection
Agency
Office of Water
Washington, D.C.
EPA 832-F-00-073
September 2000
Collection Systems
Technology Fact Sheet
Sewers, Lift Station
DESCRIPTION
Wastewater lift stations are facilities designed to
move wastewater from lower to higher elevation
through pipes. Key elements of lift stations include
a wastewater receiving well (wet-well), often
equipped with a screen or grinding to remove
coarse materials; pumps and piping with associated
valves; motors; a power supply system; an
equipment control and alarm system; and an odor
control system and ventilation system.
Lift station equipment and systems are often
installed in an enclosed structure. They can be
constructed on-site (custom-designed) or prefabricated.
Lift station capacities from
76 liters per minute (20 gallons per minute) to more
than 378,500 liters per minute (100,000 gallons per
minute). Pre-fabricated lift stations generally have
capacities of up to 38,000 liters per minute (10,000
gallons per minute). Centrifugal pumps are
commonly used in lift stations. A trapped air
column, or bubbler system, that senses pressure and
level is commonly used for pump station control.
Other control alternatives include electrodes placed
at cut-off levels, floats, mechanical clutches, and
floating mercury switches. A more sophisticated
control operation involves the use of variable speed
drives.
Lift stations are typically provided with equipment
for easy pump removal. Floor access hatches or
openings above the pump room and an overhead
monorail beam, bridge crane, or portable hoist are
commonly used.
The two most common types of lift stations are the
dry-pit or dry-well and submersible lift stations. In
dry-well lift stations, pumps and valves are housed
in a pump room (dry pit or dry-well), that is easily
accessible. The wet-well is a separate chamber
attached or located adjacent to the dry-well (pump
room) structure. Figures 1 and 2 illustrate the two
types of pumps.
Submersible lift stations do not have a separate
pump room; the lift station header piping,
associated valves, and flow meters are located in a
separate dry vault at grade for easy access.
Submersible lift stations include sealed pumps that
operate submerged in the wet-well. These are
removed to the surface periodically and reinstalled
using guide rails and a hoist. A key advantage of
dry-well lift stations is that they allow easy access
for routine visual inspection and maintenance. In
general, they are easier to repair than submersible
pumps. An advantage of submersible lift stations is
that they typically cost less than dry-well stations
and operate without frequent pump maintenance.
Submersible lift stations do not usually include
Dry Well
Wet Well
Inlet
Hoist
Discharge
Source: Qasim, 1994.
FIGURE 1 DRY-WELL PUMP
large aboveground structures and tend to blend in
with their surrounding environment in residential
areas. They require less space and are easier and
less expensive to construct for wastewater flow
capacities of 38,000 liters per minute (10,000
gallons per minute) or less.
APPLICABILITY
Lift stations are used to move wastewater from
lower to higher elevation, particularly where the
elevation of the source is not sufficient for gravity
flow and/or when the use of gravity conveyance
will result in excessive excavation depths and high
sewer construction costs.
Current Status
Lift stations are widely used in wastewater
conveyance systems. Dry-well lift stations have
been used in the industry for many years. However,
the current industry-wide trend is to replace drywell
lift stations of small and medium size
(typically less than 24,000 liters per minute or 6,350
gallons per minute) with submersible lift stations
mainly because of lower costs, a smaller footprint,
and simplified operation and maintenance.
Variable speed pumping is often used to optimize
pump performance and minimize power use.
Several types of variable-speed pumping equipment
are available, including variable voltage and
frequency drives, eddy current couplings, and
mechanical variable-speed drives. Variable-speed
pumping can reduce the size and cost of the wetwell
and allows the pumps to operate at maximum
efficiency under a variety of flow conditions.
Because variable-speed pumping allows lift station
discharge to match inflow, only nominal wet-well
storage volume is required and the well water level
is maintained at a near constant elevation.
Variable-speed pumping may allow a given flow
range to be achieved with fewer pumps than a
constant-speed alternative. Variable-speed stations
also minimize the number of pump starts and stops,
reducing mechanical wear. Although there is
significant energy saving potential for stations with
large friction losses, it may not justify the additional
capital costs unless the cost of power is relatively
high. Variable speed equipment also requires more
room within the lift station and may produce more
noise and heat than constant speed pumps.
Lift stations are complex facilities with many
auxiliary systems. Therefore, they are less reliable
than gravity wastewater conveyance. However, lift
station reliability can be significantly improved by
providing stand-by equipment (pumps and controls)
and emergency power supply systems. In addition,
lift station reliability is improved by using non-clog
pumps suitable for the particular wastewater quality
and by applying emergency alarm and automatic
control systems.
ADVANTAGES AND DISADVANTAGES
Advantages
Lift stations are used to reduce the capital cost of
sewer system construction. When gravity sewers
are installed in trenches deeper than three meters
(10 feet), the cost of sewer line installation
increases significantly because of the more complex
and costly excavation equipment and trench shoring
techniques required. The size of the gravity sewer
lines is dependent on the minimum pipe slope and
flow. Pumping wastewater can convey the same
flow using smaller pipeline size at shallower depth,
and thereby, reducing pipeline costs.
Hoist
Discharge
Source: Qasim, 1994.
FIGURE 2 WET-WELL SUBMERSIBLE
Disadvantages
Compared to sewer lines where gravity drives
wastewater flow, lift stations require a source of
electric power. If the power supply is interrupted,
flow conveyance is discontinued and can result in
flooding upstream of the lift station, It can also
interrupt the normal operation of the downstream
wastewater conveyance and treatment facilities.
This limitation is typically addressed by providing
an emergency power supply.
Key disadvantages of lift stations include the high
cost to construct and maintain and the potential for
odors and noise. Lift stations also require a
significant amount of power, are sometimes
expensive to upgrade, and may create public
concerns and negative public reaction.
The low cost of gravity wastewater conveyance and
the higher costs of building, operating, and
maintaining lift stations means that wastewater
pumping should be avoided, if possible and
technically feasible. Wastewater pumping can be
eliminated or reduced by selecting alternative sewer
routes or extending a gravity sewer using direction
drilling or other state-of-the-art deep excavation
methods. If such alternatives are viable, a costbenefit
analysis can determine if a lift station is the
most viable choice.
DESIGN CRITERIA
Cost effective lift stations are designed to: (1)
match pump capacity, type, and configuration with
wastewater quantity and quality; (2) provide
reliable and uninterruptible operation; (3) allow for
easy operation and maintenance of the installed
equipment; (4) accommodate future capacity
expansion; (5) avoid septic conditions and
excessive release of odors in the collection system
and at the lift station; (6) minimize environmental
and landscape impacts on the surrounding
residential and commercial developments; and (7)
avoid flooding of the lift station and the
surrounding areas.
Wet-well
Wet-well design depends on the type of lift station
configuration (submersible or dry-well) and the
type of pump controls (constant or variable speed).
Wet-wells are typically designed large enough to
prevent rapid pump cycling but small enough to
prevent a long detention time and associated odor
release.
Wet-well maximum detention time in constant
speed pumps is typically 20 to 30 minutes. Use of
variable frequency drives for pump speed control
allows wet-well detention time reduction to 5 to 15
minutes. The minimum recommended wet-well
bottom slope is to 2:1 to allow self-cleaning and
minimum deposit of debris. Effective volume of
the wet-well may include sewer pipelines,
especially when variable speed drives are used.
Wet-wells should always hold some level of sewage
to minimize odor release. Bar screens or grinders
are often installed in or upstream of the wet-well to
minimize pump clogging problems.
Wastewater Pumps
The number of wastewater pumps and associated
capacity should be selected to provide headcapacity
characteristics that correspond as nearly as
possible to wastewater quantity fluctuations. This
can be accomplished by preparing pump/pipeline
system head-capacity curves showing all conditions
of head (elevation of a free surface of water) and
capacity under which the pumps will be required to
operate.
The number of pumps to be installed in a lift station
depends on the station capacity, the range of flow
and the regulations. In small stations, with
maximum inflows of less than 2,640 liters per
minute (700 gallons per minute), two pumps are
customarily installed, with each unit able to meet
the maximum influent rate. For larger lift stations,
the size and number of pumps should be selected so
that the range of influent flow rates can be met
without starting and stopping pumps too frequently
and without excessive wet-well storage.
Depending on the system, the pumps are designed
to run at a reduced rate. The pumps may also
alternate to equalize wear and tear. Additional
pumps may provide intermediate capacities better
matched to typical daily flows. An alternative
option is to provide flow flexibility with variablespeed
pumps.
For pump stations with high head-losses, the singlepump
flow approach is usually the most suitable.
Parallel pumping is not as effective for such
stations because two pumps operating together yield
only slightly higher flows than one pump. If the
peak flow is to be achieved with multiple pumps in
parallel, the lift station must be equipped with at
least three pumps: two duty pumps that together
provide peak flow and one standby pump for
emergency backup. Parallel peak pumping is
typically used in large lift stations with relatively
flat system head curves. Such curves allow
multiple pumps to deliver substantially more flow
than a single pump. The use of multiple pumps in
parallel provides more flexibility.
Several types of centrifugal pumps are used in
wastewater lift stations. In the straight-flow
centrifugal pumps, wastewater does not change
direction as it passes through the pumps and into
the discharge pipe. These pumps are well suited for
low-flow/high head conditions. In angle-flow
pumps, wastewater enters the impeller axially and
passes through the volute casing at 90 degrees to its
original direction (Figure 3). This type of pump is
appropriate for pumping against low or moderate
heads. Mixed flow pumps are most viable for
pumping large quantities of wastewater at low head.
In these pumps, the outside diameter of the impeller
is less than an ordinary centrifugal pump, increasing
flow volume.
Ventilation
Ventilation and heating are required if the lift
station includes an area routinely entered by
personnel. Ventilation is particularly important to
prevent the collection of toxic and/or explosive
gases. According to the Nation Fire Protection
Association (NFPA) Section 820, all continuous
ventilation systems should be fitted with flow
detection devices connected to alarm systems to
indicate ventilation system failure. Dry-well
ventilation codes typically require six continuous
air changes per hour or 30 intermittent air changes
per hour. Wet-wells typically require 12 continuous
air changes per hour or 60 intermittent air changes
per hour. Motor control center (MCC) rooms
should have a ventilation system adequate to
provide six air changes per hour and should be air
conditioned to between 13 and 32 degrees Celsius
(55 to 90 degrees F). If the control room is
combined with an MCC room, the temperature
should not exceed 30 degrees C or 85 degrees F.
All other spaces should be designed for 12 air
changes per hour. The minimum temperature
should be 13 degrees C (55 degrees F) whenever
chemicals are stored or used.
Odor Control
Odor control is frequently required for lift stations.
A relatively simple and widely used odor control
alternative is minimizing wet-well turbulence. More
effective options include collection of odors
generated at the lift station and treating them in
scrubbers or biofilters or the addition of odor
control chemicals to the sewer upstream of the lift
station. Chemicals typically used for odor control
include chlorine, hydrogen peroxide, metal salts
(ferric chloride and ferrous sulfate) oxygen, air, and
potassium permanganate. Chemicals should be
Source: Lindeburg, revised edition 1995.
FIGURE 3 CENTRIFUGAL ANGLE-FLOW
PUMP
closely monitored to avoid affecting downstream
treatment processes, such as extended aeration.
Power Supply
The reliability of power for the pump motor drives
is a basic design consideration. Commonly used
methods of emergency power supply include
electric power feed from two independent power
distribution lines; an on-site standby generator; an
adequate portable generator with quick connection;
a stand-by engine driven pump; ready access to a
suitable portable pumping unit and appropriate
connections; and availability of an adequate holding
facility for wastewater storage upstream of the lift
station.
PERFORMANCE
The overall performance of a lift station depends on
the performance of the pumps. All pumps have
four common performance characteristics: capacity,
head, power, and overall efficiency. Capacity (flow
rate) is the quantity of liquid pumped per unit of
time, typically measured as gallons per minute
(gpm) or million gallons per day (mgd). Head is
the energy supplied to the wastewater per unit
weight, typically expressed as feet of water. Power
is the energy consumed by a pump per unit time,
typically measured as kilowatt-hours. Overall
efficiency is the ratio of useful hydraulic work
performed to actual work input. Efficiency reflects
the pump relative power losses and is usually
measured as a percentage of applied power.
Pump performance curves (Figure 4) are used to
define and compare the operating characteristics of
a pump and to identify the best combination of
performance characteristics under which a lift
station pumping system will operate under typical
conditions (flows and heads). Pump systems
operate at 75 to 85 percent efficiency most of the
time, while overall pump efficiency depends on the
type of installed pumps, their control system, and
the fluctuation of influent wastewater flow.
Performance optimization strategies focus on
different ways to match pump operational
characteristics with system flow and head
requirements. They may include the following
options: adjusting system flow paths installing
variable speed drives; using parallel pumps
installing pumps of different sizes trimming a pump
impeller; or putting a two-speed motor on one or
more pumps in a lift station. Optimizing system
performance may yield significant electrical energy
savings.
OPERATION AND MAINTENANCE
Lift station operation is usually automated and does
not require continuous on-site operator presence.
However, frequent inspections are recommended to
ensure normal functioning and to identify potential
problems. Lift station inspection typically includes
observation of pumps, motors and drives for
unusual noise, vibration, heating and leakage, check
of pump suction and discharge lines for valving
arrangement and leakage, check of control panel
switches for proper position, monitoring of
discharge pump rates and pump speed, and
monitoring of the pump suction and discharge
pressure. Weekly inspections are typically
conducted, although the frequency really depends
on the size of the lift station.
If a lift station is equipped with grinder bar screens
to remove coarse materials from the wastewater,
these materials are collected in containers and
disposed of to a sanitary landfill site as needed. If
the lift station has a scrubber system for odor
control, chemicals are supplied and replenished
typically every three months. If chemicals are
added for odor control ahead of the lift station, the
0
10
20
30
40
50
60
70
0 0.05 0.1 0.15 0.2 0.25 0.3 0.35 0.4
Discharge (m3/s)
Head (m)
System Curve
Pump Curve
Source: Adapted from Roberson and Crowe, 1993.
FIGURE 4 PUMP PERFORMANCE CURVE
chemical feed stations should be inspected weekly
and chemicals replenished as needed.
The most labor-intensive task for lift stations is
routine preventive maintenance. A well-planned
maintenance program for lift station pumps
prevents unnecessary equipment wear and
downtime. Lift station operators must maintain an
inventory of critical spare parts. The number of
spare parts in the inventory depends on the critical
needs of the unit, the rate at which the part normally
fails, and the availability of the part. The operator
should tabulate each pumping element in the system
and its recommended spare parts. This information
is typically available from the operation and
maintenance manuals provided with the lift station.
COSTS
Lift station costs depend on many factors, including
(1) wastewater quality, quantity, and projections;
(2) zoning and land use planning of the area where
the lift station will be located; (3) alternatives for
standby power sources; (4) operation and
maintenance needs and support; (5) soil properties
and underground conditions; (6) required lift to the
receiving (discharge) sewer line; (7) the severity of
impact of accidental sewage spill upon the local
area; and (8) the need for an odor control system.
These site and system specific factors must be
examined and incorporated in preparing a lift
station cost estimate.
Construction Costs
The most important factors influencing cost are the
design lift station capacity and the installed pump
power. Another cost factor is the lift station
complexity. Factors which classify a lift station as
complex include two or more of the following: (1)
extent of excavation; (2) congested site and/or
restricted access; (3) rock excavation; (4) extensive
dewatering requirements, such as cofferdams; (5)
site conflicts, including modification or removal of
existing facilities; (6) special foundations, including
piling; (7) dual power supply and on-site switch
stations and emergency power generator; and (8)
high pumping heads (design heads in excess of
200 ft).
Mechanical, electrical, and control equipment
delivered to a pumping station construction site
typically account for 15 to 30 percent of total
construction costs. Lift station construction has a
significant economy-of-scale. Typically, if the
capacity of a lift station is increased 100 percent,
the construction cost would increase only 50 to 55
percent. An important consideration is that two
identical lift stations will cost 25 to 30 percent more
than a single station of the same combined capacity.
Usually, complex lift stations cost two to three
times more than more simple lift stations with no
construction complications.
Table 1 provides examples of complex lift stations
and associated construction costs in 1999 dollars.
TABLE 1 LIFT STATION CONSTRUCTION COSTS
Lift Station
Design Flowrate
(MGD)
Operation and Maintenance Costs
Lift station operation and maintenance costs include
power, labor, maintenance, and chemicals (if used
for odor control). Usually, the costs for solids
disposal are minimal, but are included if the lift
station is equipped with bar screens to remove
coarse materials from the wastewater. Typically,
power costs account for 85 to 95 percent of the total
operation and maintenance costs and are directly
proportional to the unit cost of power and the actual
power used by the lift station pumps. Labor costs
average 1 to 2 percent of total costs. Annual
maintenance costs vary, depending on the
complexity of the equipment and instrumentation.
other websites we recommend you look at:
Address:
Callahan Pumps
5508 Wilmin Way
Suite # 4
Zip Code: 32207
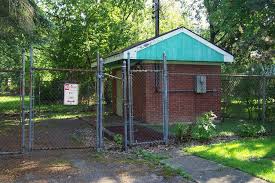
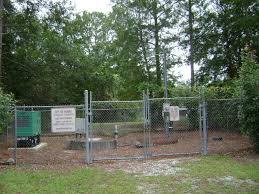
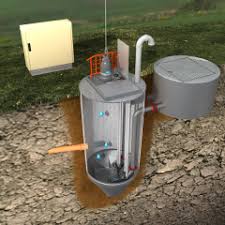
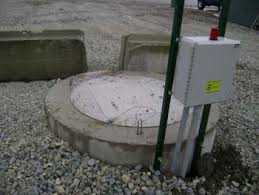
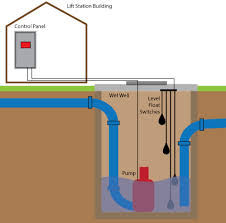